The Indian logistics industry contributes more than 15 lakh crores to the economy and employs more than 40 million people. Yet, it is not immune to supply chain disruptions. While some disturbances can be predicted and prevented, others cannot. Unforeseen disruptions, caused by the pandemic, for instance, impacted economic growth, competitiveness and employment. The Indian Chamber of Commerce stated that during the lockdown, which was followed by the first wave of the COVID-19 pandemic, the Indian logistics sector lost about ?50,000 crores, hampering the business cycles and supply chains across the country. According to an article in The Economics Times, the lockdown resulted in an increase in stuck shipments by 9%, an increase in order delays by 21% and a decline in deliveries by 9%. The pandemic took a toll on the freight capacity along with the capacity of small trucking businesses that did not have any backup plans, recovery plans or intermittent operation plans.
As the world continues to cope with and adapt to the consequences of the pandemic, the logistics industry is gradually equipping itself to be better prepared for future mishaps and disruptions.
Causes of supply chain disruptions
Supply chain disruptions can be caused by several factors, and no organisation is immune to them. Some of the prominent causes are -
- Natural Disasters and Pandemics
Natural disasters like floods, hurricanes, wildfires, earthquakes along with pandemics like COVID-19 have the potential to disrupt supply chains despite their sturdiness and strong foundation. In 2005, for example, Hurricane Katrina caused massive supply chain disruptions by hampering power and transportation routes along the Gulf Coast of the US.
- Transportation Issues
Transportation issues like increased fuel prices, cargo theft, shipping charges, route efficiencies and port complications affect the smooth functioning of supply chains. Other issues may include factors such as political upheavals and union troubles.
- Outdated Technology
Outdated technology and manual methods of working can cause disturbances in the supply chain. Organisations that have not yet adopted modern technology may experience the disruptions caused by using obsolete technology, thereby paving a way for embracing Industry 4.0.
These supply chain disruptions have an impact on the companies as well as consumers. Companies are likely to face shortages in key components and parts, resulting in delayed operations and the high cost of raw materials. Increased prices and shipment cancellations by exporters lead to an increased price of the finished product for consumers., Thus, organisations need to examine the causes of supply chain disruptions as well as their impact on the overall working of the sector and be prepared to effectively tackle such challenges.
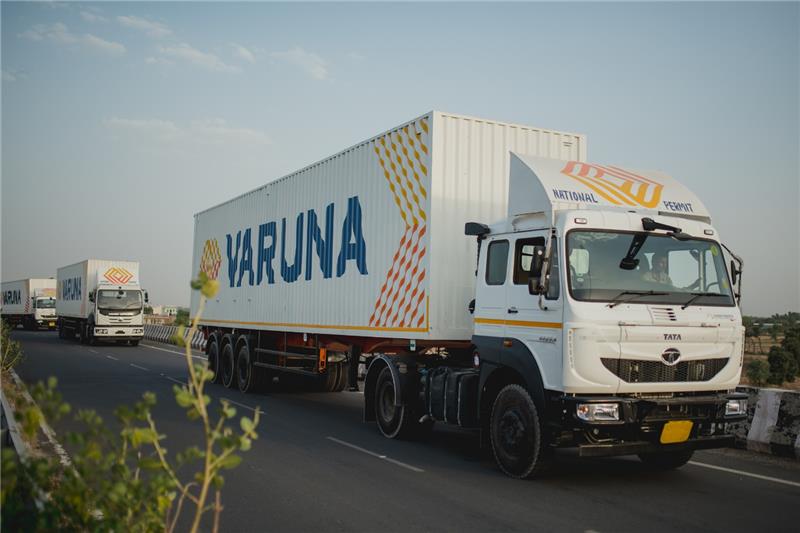
Responding to Supply Chain Disruptions
Having assessed the causes of supply chain disruptions and their impact on suppliers and consumers, organisations must focus on the appropriate ways to respond to them -
- Restructuring supply chains
When organisations are faced with disruptions and crises, they must pause, reflect and take appropriate actions. Businesses must then evaluate the critical components of their supply chains and estimate their available inventory so that they can assess the potential risks and implications and restructure their plans accordingly. This is, especially, effective when operations are hampered due to calamities, natural or otherwise, and resources need to be redistributed to produce optimal outcomes.
- Using resources optimally
Analysing network models and capabilities will help the industry be better prepared and equipped for the future by exploring different options to distribute their resources optimally. For instance, negotiating for lower prices with carriers and controlling fuel expenses can help organisations make smart investments. Additionally, partnering with logistics providers experts and identifying backup suppliers rather than relying on only a single supplier will help organisations be better prepared for unforeseen disruptions.
- Investing in technology
Investing in proper infrastructure and technology will help the sector to cut costs, increase productivity and margins and make operations smoother. Leveraging technology will help the industry to foresee potential disruptions and plan strategies to mitigate future risks.
- Training the Workforce
The workforce must be equipped to understand the new ways of working post disruptions. Organisations must upskill their employees, promote digital and data literacy as well as encourage them to become flexible to change. Empowering employees by developing their cognitive skills will prepare them to deal with unforeseen situations and respond actively.
While the industry is responding well to supply chain disruptions, it is also essential to prepare for the future and take adequate measures.
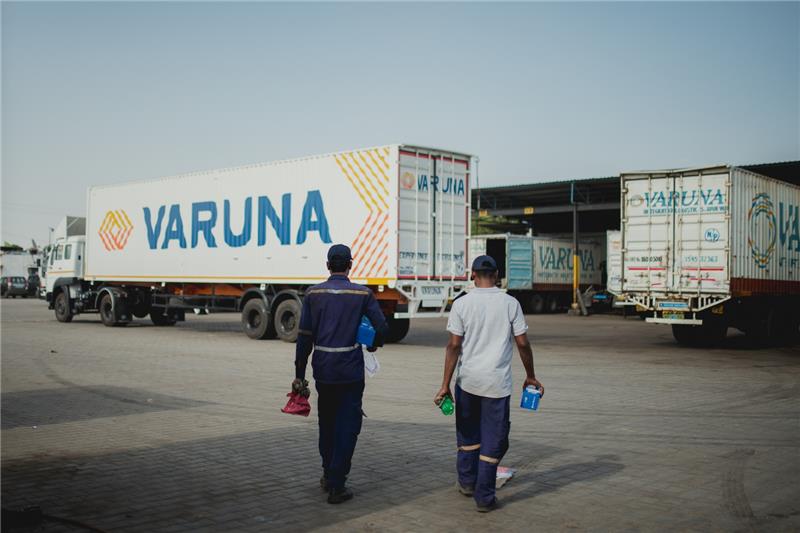
Using 3Rs to minimize the effect of supply chain disruptions
The 3Rs- Resilience, Reliance and Risk evaluation - can help organisations minimize the damages caused by supply chain disruptions. These competencies not only empower organisations to become better and more robust but also help them reduce losses by taking the right measures.
- Resilience
Organisations must analyses their readiness in times of crisis and prepare a business continuity plan along with emergency alternatives. Rethinking existing strategies and plans, reallocating its resources deliberately and collaborating and managing meaningful business relationships will ensure that the industry is prepared for future disruptions.
- Self-Reliance
Many organisations are trying to shorten or diversify themselves and their operations by becoming reliant or adopting alternative partners. This will benefit countries with the required capabilities and capacities rather than relying on others. For instance, The Government of India’s initiative, Atmanirbhar Bharat launched amidst the COVID-19 pandemic aims to boost Micro, Small and Medium Enterprises (MSMEs).
- Risk Evaluation
Organisations must be better equipped and prepared for the future by evaluating their existing models and predicting the plausibility of risks and disruptions caused in the supply chain. It is essential for businesses to identify the risks, assess and monitor them. While not all potential risks can be determined beforehand, such as the coronavirus pandemic, risk evaluation can prevent companies from being in a vulnerable position during crises.
In Conclusion
Organisations are taking conscious measures to gradually become more equipped and prompt in dealing with the various kinds of disruptions by evolving their supply chains with the changing market landscape and introducing more efficient technology to improve operations. The market has come a long way from facing the brunt of the COVID-19 pandemic to adapting, adjusting and preparing itself for the future. These increased insights have helped organisations to redesign, transform and grow as they develop their competencies and reduce their dependence on other sources.